The most common mistake in effectively implement Service & Asset Management and, therefore, achieve excellence and production efficiency, is the effort to understand and analyse the financial information without perceiving or processing the necessary technical details and technical teams’ actions which correlate the daily behaviour of the facility with the financial numbers.
In addition, Asset Management is being considered as a separate activity which overviews all the other activities but it is separate by the management of the Technical teams or it is performed by financial managers.
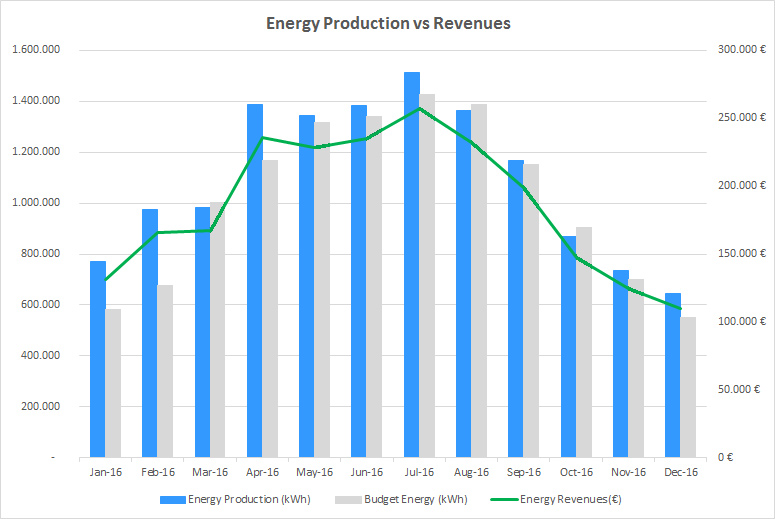
Redefining Service & Asset Management: Bridging the gap
Enerdia re-defines Service and Asset Management as a fundamental procedure of the Energy facility which combines all activities concerning the facilities in order to generate growth and success for the Investor.
As a result, efficient Service & Asset Management combines the following

Culture
It must enhance culture and bonds between the Investor, the Asset Manager, the O&M and all the Asset’s stakeholders. It therefore must connect every action of the Technical teams, with every Equipment installed inside the Facility and the financial expectations of the Investor.

Bridge the gap
It must create a common language between the Technical and Financial teams in such way that every action and therefore, every reaction, to efficiently promote the goals of the investement.

Knowledge Sharing
Knowledge is the key for O&M efficiency. As a result, knowledge and best technical practices should flow between all stakeholders of the investment in such a way that, good practice is further excelled and at the same time it will remain as an asset of the investor ensuring the long-life of the investment, independently of the O&M personnel.

Accurate guidelines for Success
Why, how much, when, if, how and who. Those questions must be easily answered by the Asset Management activity at any given time of the investment life-cycle, and at the same time, to promote clear guidelines for decision making.

Resources Management
It must continuously be able to track and analyze all available resources’ performance and capabilities in order to effectively allocate them in the best combination for production maximization and O&M efficiency.

Tangible KPIs
We need reliable, tangible and transparent methods to assist the Energy Investor to easily identify if and which of his asset’s resources do not return their maximum potential or capabilities, in terms of production efficiency and revenues.
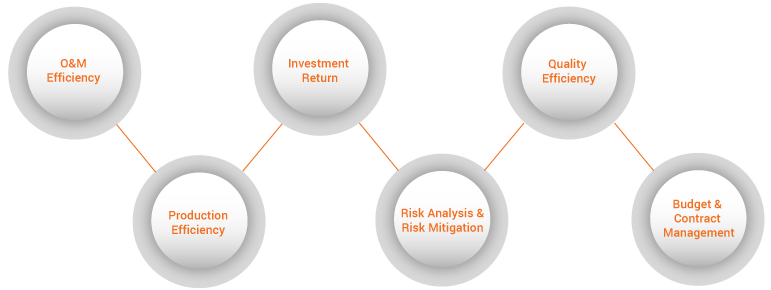
Achieving Asset Excellence
Excellence is achieved only when the information related to the financial success of the facility is equally distributed among all the stakeholders and contractors and, at the same time, the outcome of the Service & Asset Management procedure offers:

Facility Service Book
Analytical Historical behavioural information of the Facility

Analytical Ticketing System
Clear and tangible resources allocation system and reporting.

Equipment Correlation
All facilities related actions are directly connected to its installed Equipment and components.

No Misleading Information
The Service & Asset management reporting reflects all equipments’ behavioural analysis as well as the technical teams’ efficiency vs production efficiency.
We achieve Service & Asset Excellence guarantying investment over-performance and financial growth through:
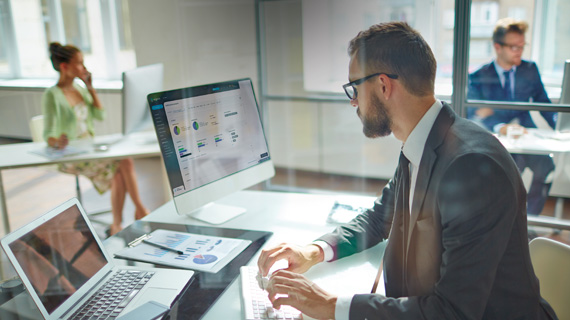